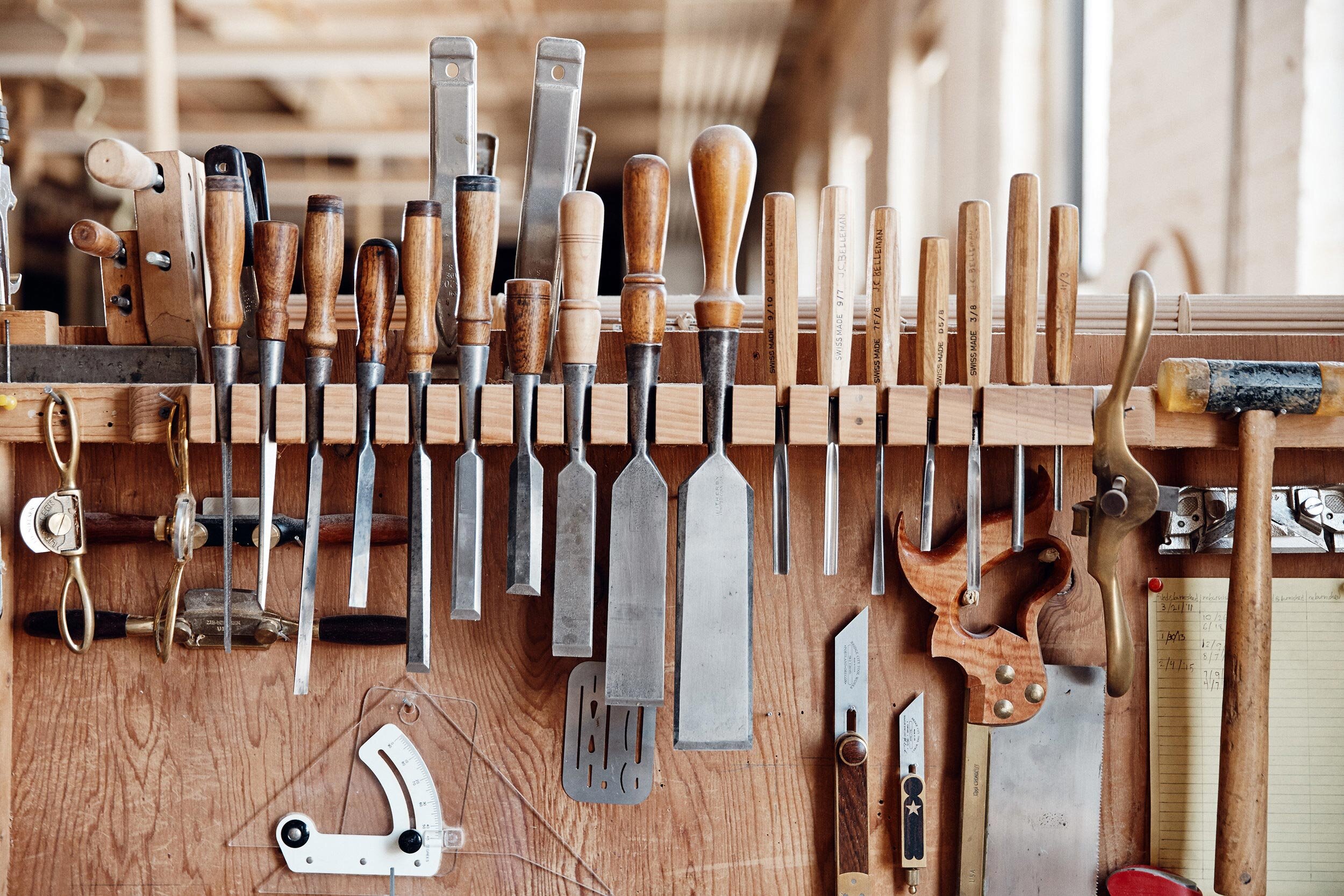
Version 1.0
Building product information
Designated building product: Class 2
In this guide
Freear Philip Ltd, trading as Well Hung Joinery has provided this declaration to satisfy the provisions of Schedule 1(d) of the Building (Building Product Information Requirements) Regulations 2022.
As a consumer it is always important to have a full understanding of the products you are selecting for your project. Below, is a full breakdown of how Well Hung Joinery Timber Joinery complies with the NZ Building Code.
Product/system
Name:
Well Hung Joinery Timber Joinery
Line:
Well Hung Joinery Timber Joinery comprising of a full suite of timber window and door joinery units.
Well Hung Joinery Timber Joinery has been designed for, but is not limited to, use in timber-framed residential housing.
Well Hung Joinery Timber Joinery is custom fabricated to the requirements of each project. Units are glazed typically with insulated glass units (IGU's), although single glazing may also be requested in certain conditions.
Well Hung Joinery Timber Joinery may include fixed or opening sashes and door panels, and constructed in various forms such as: Awning, Casement, Double hung, Sliding and Bifold styles. Door systems may include: Hinged, Bifold and Sliding.
Identifier:
Well Hung Joinery Timber Joinery
Description
Well Hung Joinery Timber Joinery is typically built out of Pine frames, although other species of timber can also be used. Typically, our doors and sashes are built out of Red Cedar, Yellow Cedar, or thermally modified Pine (such as Accoya or Thermofixx).
Well Hung Joinery Timber Joinery has been designed for but is not limited to, use in timber-framed residential housing.
Well Hung Joinery Timber Joinery is custom fabricated to the requirements of each project. Units are glazed typically with insulated glass units (IGUs), although single glazing may also be requested in certain conditions.
Well Hung Joinery Timber Joinery is by nature Thermally Broken.
The minimum R-Values of Timber Joinery are R0.46, however, we can achieve higher R-Values by adding in Low E Glass and/or Argon Gas into our insulated glazing units (IGUs).
Well Hung Joinery Timber Joinery glass typically has a light transmittance value of between 80% and 90%, depending on the glass type specified.
Well Hung Joinery Timber Joinery glass meets the NZS safety requirements of NZS:4223.3:2016.
Well Hung Joinery Timber Joinery can be built as part of the JMF suite of joinery.
Further information about this suite of joinery can be found at www.jmfnz.co.nzWell Hung Joinery Timber Joinery comprising of a full suite of timber windows and door joinery units.
Well Hung Joinery Timber Joinery may include fixed or opening sashes and door panels, and constructed in various forms such as: Awning, Casement, Double Hung, Sliding and Bifold styles. Door systems may include: Hinged, Bifold and Sliding. For a full description of all model types, go to www.wellhungjoinery.co.nz/home#product-range
Well Hung Joinery Timber Joinery are not fire-rated and cannot be used where Fire Ratings are required unless stated in C/AS1 and C/AS2.
Scope of use
Well Hung Joinery Timber Joinery is designed for, but is not limited to, use in projects within the following scope:
Housing and residential buildings, and their associated ancillary and outbuildings.
Timber framed, steel framed or concrete construction.
All Wind Zones up to and including Extra High.
All Exposure Zones, except in microclimates where there is evidence of corrosion in adjacent structures caused by industrial or geothermal atmospheres.
Overall door or window size up to 6m wide x 3m high, with a maximum unit weight of 180kg. Limitations on the configuration, maximum dimensions, and weights of individual panels also apply and are dependent on the panel type.
Maximum IGU thickness is 26mm.
Design and installation that follows common Acceptable Solutions such as E2/AS1, F4/AS1, G4/AS1, G7/AS1 and H1/AS1.
Frames may be built out of either paint-quality timbers or stain-quality timbers. Doors and sashes may be built out of either paint-quality timbers or stain-quality timbers.
Well Hung Joinery Timber Joinery may be used in projects outside this scope if other parties such as architects or cladding system suppliers establish appropriate design and installation requirements.
Well Hung Joinery Timber Joinery is custom fabricated to the requirements of each project. Prior to fabrication, the following project selections must be confirmed by the specifier:
Unit size.
Opening panel size(s) and type(s), and configuration of fixed and opening panels, including any specific requirements for doors that are on access routes or escape routes.
Project Wind Zone.
Project Exposure Zone.
IGU performance selections, including R-Value and safety glazing requirements.
Safety fittings and hardware: restrictors, door closers and swimming pool barrier latches to be fitted where an opening window or door requires features for safety from falling or is within a wall that forms part of a residential pool barrier.
Finish requirements timber material selections. Default specification for frames is pre-primed finger-jointed radiata pine H3.1 treated, suitable for paint finish. Default specification for doors and sashes is either Red or Yellow Cedar, or chemically modified Pine.
Conditions of use
Well Hung Joinery Timber Joinery:
Must be used with buildings within the Scope of E2/AS1, Third Edition 10 paras 1.1, 1.1.1 and 1.2.1.
Must be installed with claddings and details as described in E2/AS1.
Must be used with buildings located in Wind Zones up to an including Extra High (as defined in NZS 3604:2011 (Timber Framed buildings).
Can be used in all Exposure Zones excluding microclimates.
Must be installed in accordance with the JMFNZ Installation Manuals.
Calculation of window areas for the purpose of G7 must be done in accordance with G7/AS1.
When calculating the opening areas of the Well Hung Joinery Timber Joinery for ventilation purposes, areas must be in accordance with G4/AS1.
Must be installed by a licensed building practitioner.
Not able to be used where there are fire rating requirements.
Not to be used in roofs.
Must be designed in accordance with JMFNZ profiles and installation requirements.
Ensure that the joinery is protected from dust, debris, and moisture if stored prior to installation.
Inspect joinery thoroughly before beginning installation to ensure it is free from any defects and damage, including damage caused during transit and delivery.
Check the dimensions and fit of each unit against the rough opening.
Install the door in accordance with the consented or design drawings and with JMFNZ installation requirements available from www.jmfnz.co.nz
Ensure door and window units are installed plumb, level, and in-plane, within the tolerances set out in the MBIE Guide to materials, tolerances, and workmanship in residential construction.
Check and adjust all seals and operating hardware to ensure good fit and proper operation and function without jamming or gaps.
Ensure drain holes are clear of dirt and debris following installation.
Relevant building code clauses
B1 Structure: B1.3.1, B1.3.2, B1.3.3 (a, b, h, j), B1.3.4
B2 Durability: B2.3.1 (b, c)
E2 External moisture: E2.3.2, E2.3.7
F2 Hazardous building materials: F2.3.1, F2.3.3
G4 Ventilation: G4.3.1
G7 Natural light: G7.3.1, G7.3.2
H1 Energy efficiency: H1.3.1 (a, b), H1.3.2E
Contributions to compliance
B1 Structure: Well Hung Joinery Timber Joinery has been tested in accordance with NZS 4211:2008, and is fabricated to the structural requirements of the Wind Zone specified in the project requirements. Well Hung Joinery Timber Joinery is glazed to comply with NZS 4223.3:2016 where specified in the project requirements because human impact may occur.
B2 Durability: Well Hung Joinery Timber Joinery can be finished to provide a durability of at least 15 years in all Exposure Zones, except in microclimates where there is evidence of corrosion in adjacent structures caused by industrial or geothermal atmospheres. Durability is dependent on Well Hung Joinery Timber Joinery being installed and maintained in accordance with standard JMF requirements. IGUs comply with the requirements of NZS 4223.2: 2016. Timber reveals comply with NZS 3602:2003
E2 External Moisture: Well Hung Joinery Timber Joinery has been tested in accordance with NZS 4211:2008 and is fabricated to the water penetration requirements of the Wind Zone specified in the project requirements. Well Hung Joinery Timber Joinery is suitable for installation in accordance with Acceptable Solution E2/AS1 and in accordance with installation details set out on the JMF website. These can be viewed at www.jmfnz.co.nz/installation-preparation-information. Installation details provided by other parties such as architects and cladding system suppliers may also be suitable.
E3.3.1: Well Hung Joinery Timber Joinery is glazed with IGUs to the project requirements, and does not require condensation collection channels to meet the requirements of E3/AS1 Second Edition Amendment 7, Paragraph 1.3 Condensation control.
F2 Hazardous Building Materials: Well Hung Joinery Timber Joinery is safe when handled in accordance with installation instructions. Well Hung Joinery Timber Joinery is fabricated to comply with NZS 4223.3:2016 where specified in the project requirements.
F4.3.1 and F4.3.4: Well Hung Joinery Timber Joinery is fabricated with opening restrictors to comply with F4/AS1 Third Edition Amendment 2, Paragraph 2.0 Opening Windows, where relevant considerations are specified in the project requirements.
F9.3.4: Well Hung Joinery Timber Joinery may be fabricated with restrictors, door closers and swimming pool barrier latches fitted to opening windows or doors within a wall that forms part of a residential pool barrier. Residential pool barrier designs may comply with F9/AS1 First Edition, or with an alternative design provided by other parties. Well Hung Joinery Timber Joinery does not include warning signs and door alarms: if these are required by the design then they may be supplied and installed on-site by others.
G4 Ventilation: Well Hung Joinery Timber Joinery can be fabricated with opening sashes of the type and dimensions specified in the project requirements to help provide building ventilation. Ventilation design may comply with G4/AS1 Fourth Edition, Paragraph 1.2 Natural ventilation, or an alternative ventilation system design that utilises opening window sashes and is provided by other parties such as mechanical services engineers could be suitable.
G7 Natural Light: Well Hung Joinery Timber Joinery can be fabricated with the area and Visible Light Transmittance (VLT) of glazing specified by the project requirements to help provide natural light and awareness of the outside. Glazing design may comply with G7/AS1 Second Edition or G7/AS2 First Edition, or an alternative glazing design provided by other parties such as lighting engineers could be suitable.
H1 Energy Efficiency: Well Hung Joinery Timber Joinery can be fabricated with IGUs made from a range of possible glass, spacer and infill gas types, to suit the window insulation (R-value) requirements of the project. Depending on the window or door type, dimensions and IGU type, R-values between R0.46 and R0.77 can be provided, determined in accordance with either H1/AS1 Fifth Edition Amendment 1, Table E1.1.1, or with H1/VM1 Fifth Edition Amendment 1, Paragraph E1.
Relevant standards
Well Hung Joinery Timber Joinery, and/or its component parts, are tested, fabricated and specified to comply with the following standards, as relevant to the project specifications:
SNZ TS 4211:2016 Specification for the classification of windows (2016 classification type).
NZS 4211:2008 Specification for the performance of windows.
NZS 4223 Code of practice for glazing in buildings – Part 1:2008 Glass selection and glazing.
NZS 4223 Code of practice for glazing in buildings – Part 2:2016 Insulating glass units.
NZS 4223 Code of practice for glazing in buildings – Part 3:2016 Human impact safety requirements.
NZS 4223 Code of practice for glazing in buildings – Part 4:2008 Dead, wind and snow loading.
NZS 3602:2003 Timber and wood-based products for use in buildings.
NZS 3610:1979 Profiles of mouldings and joinery.
NZS 3640:2003 Chemical preservation of round and sawn timber.
NZS 3622:2004 Verification of timber properties.
Supporting documentation
The following additional documentation supports the above statements:
JMFNZ FAQs
Including: Certification, design, installation, maintenance, test results, warranty
www.jmfnz.co.nz/technical-faqs
JMFNZ Installation and preparation information
Including: Installation, maintenance
www.jmfnz.co.nz/installation-preparation-information
JMFNZ Downloads
Including: Design, installation, maintenance, warranty
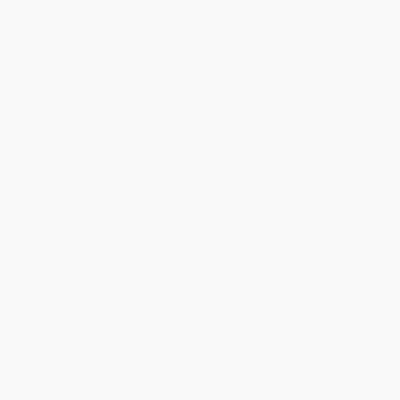
Contact details
Manufacture location
New Zealand
Legal and trading name of manufacturer
Freear Philip Ltd, trading as Well Hung Joinery
Manufacturer address for service
21 Lower Tyers Rd, Ngauranga
Wellington 6035, New Zealand
Manufacturer website
Manufacturer email
Manufacturer telephone
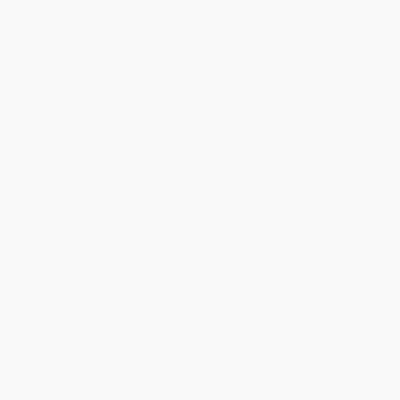
Responsible person
As the responsible person as set out in Regulation 3, I confirm that the information supplied in this declaration is based on information supplied to the company as well as the company's own processes and is therefore, to the best of my knowledge, correct.
I can also confirm that Well Hung Joinery Timber Joinery is not subject to a warning on ban under S26 of the Building Act.
Signed for and on behalf of Freear Philip Ltd, trading as Well Hung Joinery:
Manager, Well Hung Joinery
March 2024
Freear Philip Ltd, trading as Well Hung Joinery
Appendix
This appendix includes information relating to BPIR Ready.
Publishing this information is not a requirement under BPIR. Its inclusion here is to provide a reference for how this BPIR summary was generated as well as to help summary creators understand the performance clauses suggested by BPIR Ready.
BPIR Ready selections
-
• Use in an external wall to provide natural light
• Use where safety glass is required
• Provides ventilation
• Fire rating
Building code performance clauses
-
B1.3.1
Buildings, building elements and sitework shall have a low probability of rupturing, becoming unstable, losing equilibrium, or collapsing during construction or alteration and throughout their lives.
B1.3.2
Buildings, building elements and sitework shall have a low probability of causing loss of amenity through undue deformation, vibratory response, degradation, or other physical characteristics throughout their lives, or during construction or alteration when the building is in use.
B1.3.3
Account shall be taken of all physical conditions likely to affect the stability of buildings, building elements and sitework, including:
a. Self-weight
b. Imposed gravity loads arising from use
c. Wind
d. Impact
B1.3.4
Due allowances shall be made for:
a. The consequences of failure.
b. The intended use of the building.
c. Effects of uncertainties resulting from construction activities, or the sequence in which construction activities occur.
d. Variation in the properties of materials and the characteristics of the site.
e. Accuracy limitations inherent in the methods used to predict the stability of buildings.
-
B2.3.1
Building elements must, with only normal maintenance, continue to satisfy the performance requirements of this code for the lesser of the specified intended life of the building, if stated, or:
a. 15 years if: those building elements (including the building envelope, exposed plumbing in the subfloor space, and in-built chimneys and flues) are moderately difficult to access or replace, or failure of those building elements to comply with the building code would go undetected during normal use of the building, but would be easily detected during normal maintenance.
b. 5 years if: the building elements (including services, linings, renewable protective coatings, and fixtures) are easy to access and replace, and failure of those building elements to comply with the building code would be easily detected during normal use of the building.
-
E2.3.2
Roofs and exterior walls must prevent the penetration of water that could cause undue dampness, damage to building elements, or both.
E2.3.7
Building elements must be constructed in a way that makes due allowance for the following:
a. The consequences of failure.
b. The effects of uncertainties resulting from construction or from the sequence in which different aspects of construction occur.
c. Variation in the properties of materials and in the characteristics of the site.
-
F2.3.1
The quantities of gas, liquid, radiation or solid particles emitted by materials used in the construction of buildings, shall not give rise to harmful concentrations at the surface of the material where the material is exposed, or in the atmosphere of any space.
F2.3.3
Glass or other brittle materials with which people are likely to come into contact shall:
a. If broken on impact, break in a way that is unlikely to cause injury, or
b. Resist a reasonably foreseeable impact without breaking, or
c. be protected from impact.
-
G4.3.1
Spaces within buildings shall have means of ventilation with outdoor air that will provide an adequate number of air changes to maintain air purity.
-
G7.3.1
Natural light shall provide an illuminance of no less than 30 lux at floor level for 75% of the standard year.
G7.3.2
Openings to give awareness of the outside shall be transparent and provided in suitable locations.
-
H1.3.1
The building envelope enclosing spaces where the temperature or humidity (or both) are modified must be constructed to:
a. Provide adequate thermal resistance.
b. Limit uncontrollable airflow.
H1.3.2E
Buildings must be constructed to ensure that their building performance index does not exceed 1.55.